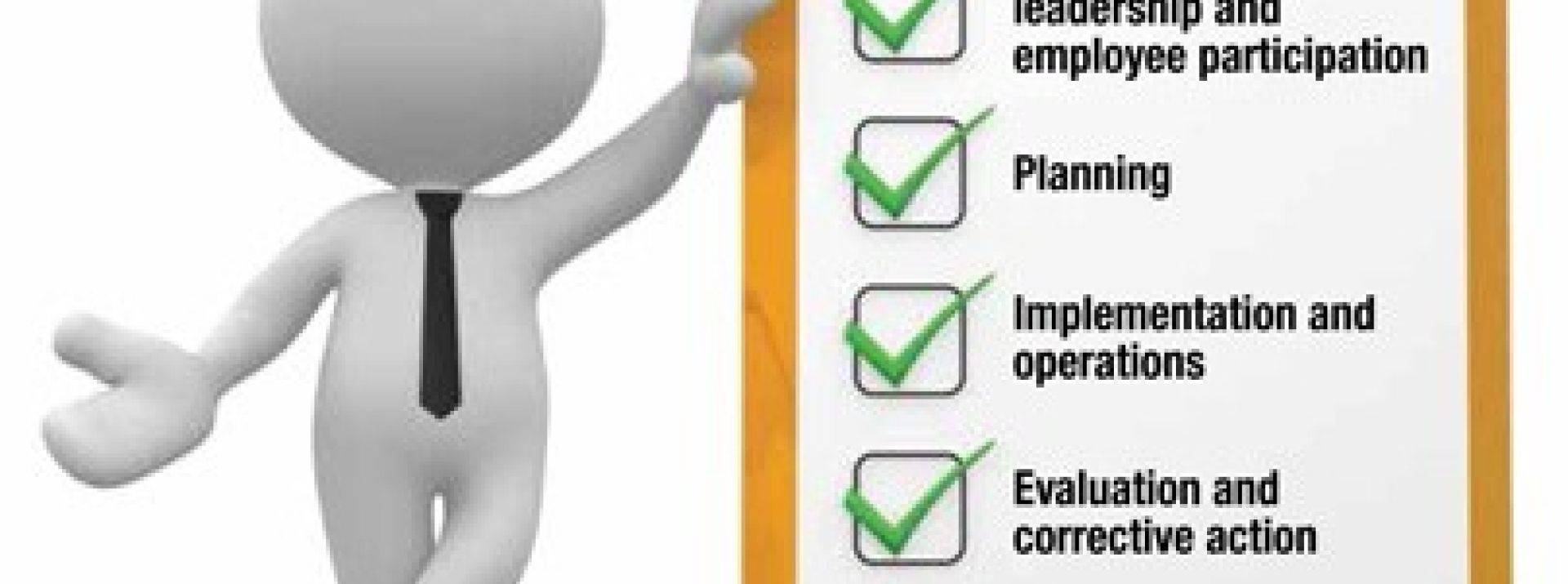
Does Your Company Have an Effective Safety Management System?
Your safety program can have fully developed rules and procedures, a top-notch training program and the best safety equipment and tools money can buy – and there is still the possibility that it may not be successful. Although these things are extremely important and necessary, safety success will not occur until your safety program becomes a fully functional safety management system. This means that everyone in the organization is actively pursuing the same safety goals and working together in a synchronized manner to achieve those goals. A fully developed and well-executed safety management system is the backbone of safety excellence.
Safety Management System Components
What does a safety management system need in order to be effective? According to ANSI/AIHA Z10-2012, “Occupational Health and Safety Management Systems,” the following components are required for success:
• Management leadership and employee participation
• Planning
• Implementation and operations
• Evaluation and corrective action
• Management review
Let’s take a closer look at how each component is defined.
Management Leadership
Management must have meaningful involvement and visible leadership, and they also must set clear roles including responsibilities, accountability and authority for the safety process. Additionally, members of management must ensure that organizational resources are provided and safety is integrated into all other business parameters, such as profitability, productivity and quality.
Employee Participation
Employees must have meaningful involvement in the development and execution of safety procedures. They must be actively engaged in the identification of hazards and risks, as well as actively participate in the planning, evaluation and implementation of control measures for their safety.
Planning
Develop plans to identify safety issues, prioritize the issues and implement plans to correct those issues. Plans must assess safety concerns and the level of risk for identified hazards, establish priorities based on the level of risk, and identify and correct underlying causes related to safety system deficiencies. Safety plans must reduce risk and improve the workplace in a measurable manner.
Implementation and Operations
Create an implementation plan to reduce risks by using controls. Establish a process to identify and address hazards during the design of equipment or facilities. Develop both a contractor safety process and an emergency response process. Define training needs and establish new and ongoing training to ensure employee competence. Communicate safety effectively and encourage employees to make recommendations to improve safety.
Evaluation and Corrective Action
Monitor, measure and assess safety performance. Implement preventive and corrective action processes and provide feedback about the planning process.
Management Review
Establish a process for top management to review the safety management system and recommend improvements to ensure the system’s continued suitability, adequacy and effectiveness.
Real-World Safety Initiative
It is critical to understand the purpose and application of each of the above components. To give the components some context, let’s review a real-world safety initiative and dissect where it went wrong from a safety management system perspective.
The Initiative
A new safety rule requires employees to tuck in their long-sleeved, arc-rated shirts when performing work that involves arc hazards. The safety department developed the rule to comply with regulatory requirements, and the new rule was communicated via safety meetings, internal communications and the safety dashboard. All affected employees were told about the rule and that safety auditors would be inspecting for rule compliance immediately.
Safety audits performed over the next several months identified members of five crews in violation of the new rule. Since the violations appeared to be widespread, the auditor followed up with all levels of management and with employees to better understand the facts surrounding the noncompliance. The following statements were taken during the audit process. Interviews were enlightening and set the stage for understanding the complexity of the noncompliance issue.
Employees: “No one told us when the rule was required so we were doing what we thought was right since we have never had a problem with arcs tunneling under our shirts.”
Frontline Crew Leader: “You can’t expect me to be responsible for their clothing – that’s their responsibility to know when and how to wear their clothing.”
Operations Supervisor: “The crew leader has more important things to do on the job than to police this crazy safety rule. Whoever developed the rule does not understand field work.”
Operations Manager: “I don’t see how I can be responsible; I am never in the field. Talk to the safety department for answers.”
Vice President of Electric Operations: “My department is very safety focused and we spend lots of money supplying PPE so our employees can be safe. I am sure it is only a few employees who are not complying.”
President/CEO: “We rarely have accidents, so I feel the numbers speak for our safety success. Our safety department does a good job of keeping people safe.”
A System Failure
So, what went wrong in this scenario? Let’s review using the components of a safety management system as our guide.
Management Leadership and Employee Participation
Leadership had no involvement, no ownership, no responsibility and no authority to ensure compliance. Also, employees had no involvement, no ownership, no understanding and no reason to comply.
Planning
Minimal thought was given to planning, implementation, communications and measurements.
Implementation and Operations
There was minimal understanding of risk, weak controls were in place, weak training was given and there was no evaluation of training effectiveness.
Evaluation and Corrective Action
No measurements were used to identify weaknesses and no corrective action plan was implemented.
Management Review
Management review was not completed for rule suitability, adequacy and effectiveness.
Safety Management System Success
Now let’s consider how this scenario may have played out had it occurred at an organization with an effective safety management system in place.
What if the senior manager fully understood the new rule requirements and held the rest of the management team accountable for a successful implementation?
What if the operations manager fully understood the requirements of the new rule and was involved with the safety department in the rule’s development; understood and communicated with his supervisors how an employee could be injured if the rule was not implemented correctly; was committed to getting his supervisor’s input and developing methods to address field challenges; developed an implementation timeline with his supervisor’s input; communicated his expectations and accountability for compliance; and held his supervisors accountable for compliance?
What if the frontline crew leader fully understood the new rule and was able to explain it to his team, as well as provide the reasons for its development, answer any questions and offer tangible solutions to any problems the rule may present? What if the frontline crew leader also understood the importance of and was committed to helping his crew be successful with the new rule; communicated with his crew regularly; coached his crew effectively about how to apply the rule; developed an implementation timeline with his crew’s input; communicated his expectations and accountability for compliance; and held his crew accountable?
What if crew members fully understood the new rule and its safety value; knew when the rule was required and how to successfully apply it; were committed to helping others be successful in their application of the rule; and held themselves accountable for complying with the rule?
If these things had happened during the course of the earlier example, interviews would not have been necessary to determine the reasons for noncompliance because noncompliance likely would not have been an issue.
Summary
Scenarios like the one referenced in this article are happening regularly in our organizations. However, many utilities also are successfully implementing initiatives within their organizations. If you were to poll electric power companies concerning safety initiatives that were successful, you would hear feedback such as management was fully on board; employees participated in the decision-making process; execution of the implementation plan went smoothly; everyone had buy-in and understood their role; and training was good. The difference between a successful safety initiative and an unsuccessful safety initiative is the strength of the organization’s safety management system. If you’re looking for more in-depth information about the components discussed in this article and how they work together as a system, refer to ANSI/AIHA Z10-2012.
About the Author: Pam Tompkins, CSP, CUSP, is president and CEO of SET Solutions and a 37-year veteran of the electric utility industry. She is a founding member of the Utility Safety & Ops Leadership Network and presently serves on the executive board. Tompkins has authored and presented technical papers on high-voltage electrical safety issues at iP conferences, IEEE workshops, ASSE conferences and for many other organizations. She is an OSHA-authorized instructor who specializes in helping electric power organizations in the U.S. and abroad comply with today’s safety and training requirements.